Dust from livestock grazing in the southwest reduces water runoff in the Colorado River Basin by 5%
An interesting study has been released by the Center for Snow and Avalanche Studies which explains that spring runoff from the Colorado Rockies has been compressed into a shorter period of time due to high levels of dust found on the mountain’s snowbanks.
“Runoff comes from the mountains in a more compressed period, which makes water management more difficult than if the water came more slowly out of the mountains.”
Evaporation and sublimation of the warmer snow itself–then transpiration from the earlier-exposed vegetation–results in water losses to the atmosphere, losses that then don’t go into runoff.
According to the study, the dust loading is five times greater than normal due to human activities such as livestock grazing, activities associated to livestock grazing such as vegetation treatments like these pictured in Nevada, and other disturbances.

Microbiotic soil crusts are crucial elements of the desert southwest. These crusts provide many important functions such as keeping soils in place, sequestering very large amounts of carbon, and protecting lands from weed invasion. Livestock grazing and the vegetation treatments, disguised as “habitat improvements” but intended to increase livestock forage, are extremely deleterious to these crusts and have resulted in cheatgrass invasion and increased fire cycles. Once the crusts are gone it takes decades, under ideal conditions, to reform. In many cases, as with cheatgrass infested areas, the crusts never reform due to continued livestock grazing and repeated fires.
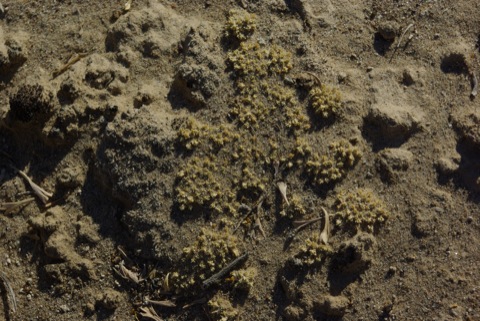
So not only does the welfare public ranching system run a $123 million deficit, it also costs 35 billion cubic feet of water to the Colorado River Basin.

Dust cuts water flow into upper Colorado River.
Los Angeles Times
Windborne Dust on High Peaks Dampens Colorado River Runoff
National Science Foundation
Images
National Science Foundation
Comments
It looks like one good wind down that wasted Nevada valley would move millions of tons of dust.
I sunk in to my ankles after I walked through the dust. It was amazing that they thought it was a good thing to totally destroy a climax habitat. I found sign of pygmy rabbits and all sorts of reptiles. What a disgrace the BLM is.
corporate-welfare ranching is a shameful disgrace.
I don’t know how more people aren’t up in arms about laying waste to large swaths of land just in the name of ranching. All that devastation for 1% of our beef production and whatever small share of sheep related industries.
The same thought crossed my mind when I was spending time around Olympic National Park this summer. I drive through Forks, which is surrounded by extensive clear-cutting for miles on end, and I see nothing but support for the logging industry. They turned what could have been a perennial source of tourism revenue for generations in old-growth forest into a clear-cut wasteland. They are probably still pissed they can’t snag the last 25% of it in the NP. I’m not kidding you, there is almost ZERO old growth left outside the park.
It’s amazing to me that the local residents will stand by Weyerhauser or Plum Creek to the death, while the company will hire and fire them all without a second thought and snatch their most valuable resource out from under them and pretend to be doing them all a favor.
Additionaly, I’m not turning a blind eye to the need for lumber, it’s just that there’s a smart way to do it (even if it causes an increase in prices), and then there’s the stupid, unsustainable, and destructive way to do it.
Daniel Berg,
I don’t know why people in these “resource dependent” communities simply let themselves be used.
Montana and Idaho timber towns and mining towns often had a strong fighting spirit that kept the corporations in line. Butte, Montana was a good example, but the grandchildren of those who stood up for worker’s rights seem to have been put on tranquilizers and their attention diverted to unpleasant conflicts over ethnicity, religion, culture, sexual orientation.
I recently read a book by K Ross Toole that talked about the old timber and mining towns of Montana and their struggles. I could hardly put the book down until it was finished.
I believe that Olympic National Forest & Washington state forest lands still have some old growth although I don’t know how much. The remaining forest lands are private & Indian owned & the current clearcutting is removing 2nd & 3rd growth forests (highly productive lands). In the last few decades new forest practices have been implemented that do a much better job of protecting soil & water. The old growth on private & Indian lands was pretty much removed 30 plus years ago. Clearcutting may not be “pretty” but if done in a RESPONSIBLE manner is not a soil & water issue in western Oregon & Washington. And I acknowledge that “clearcutting” is a highly charged emotional word & action that gets people to rioting. I am a member of a watershed council & have been following forest practices issues for 40 years & I am no friend of environmental degradation!
I believe a figure I saw was that around 25% give or take of the original old growth is still intact on the Olympic Peninsula, virtually all of it within the park or buffers. I’m not sure what the figure is on exclusively low elevation old-growth.
My statement earlier doesn’t pay homage to the changes that have gone on over the during the last couple of decades. Changes that some people have worked very hard for. I’ve been visiting the peninsula for over 20 years and it doesn’t take an expert to see that there have been changes.
Daniel Berg Says:
September 22, 2010 at 11:12 AM
Additionaly, I’m not turning a blind eye to the need for lumber, it’s just that there’s a smart way to do it (even if it causes an increase in prices), and then there’s the stupid, unsustainable, and destructive way to do it.
Daniel, I’m still wondering why, with all the new technology out there for recycling, trees are still in the mix for building materials or…… anything else?
We (as in mankind) continue to stumble around the issue of what to do with the millions, if not billions, of pounds of waste we produce every year that end up in landfills, yet we continue to allow government to ignore any start up companies, willing to address the problem if given the chance.
Nancy,
Years ago, in fact 30 years ago, I was a carpenter in Steamboat Springs. Colorado. I hate todays logging practices, but as a carpenter I have always enjoyed cutting into new wood and erecting a new structure. I would not enjoy cutting into garage.
Nancy,
I would be interested to see an analysis of the difference in cost between a residential home built using the standard amount of wood vs. a home that is specifically built not using wood whenever possible.
If the government dabbles in green technology, I hope they at least do it in an accountable way. When a start-up company only has to answer to whomever is cutting their million dollar checks at a government agency, there is a heightened risk for waste. At my old job, I audited several companies who existed solely because of government funding and wasteful spending was not infrequent.
I would not enjoy cutting into garage.
Meaning what Elk?
Nancy I read your post to fast. I thought that you wanted to use garage as a building material.
Daniel, Here is a company that is recycling carpet for buidling materials:
http://nyloboard.com/faq
Ran across another company that reclaims wood scraps. I’ve been around a few buidling sites and its amazing what ends up in landfills that could be recycled.
I have a nephew who is doing research on bamboo vs wood as a building material. It can grow in almost any climate and matures much faster than the average tree and when havested, it grows back, unlike trees.
http://greenbuildingelements.com/2010/08/11/bamboo-in-america/
One company is working with cement that can capture carbon dioxide. Perhaps there’s a use for the dust, gathered, recycled, compacted into a solid material, similar to adobe.
it seems to me, generally speaking, there ought be economic use for any “waste” and we ought ensure that level of resource efficiency.
the fact that it might seem superficially, economically cheaper to exploit a natural resource than to capture a “waste” from a pre-existing manufacturing process when that “waste” can serve the same need is a gross illustration of the extent to which our markets are skewed and divorced from the natural systems upon which ultimately they depend.
I was just listening to the radio and an add said that the typical new house has 4 tons of waste going to the landfill. If new construction generates 4 tons of landfill waste then the purchaser unknowingly is going to pay for the wasted materials. Four tons is a lot of wasted money.
That’s a huge amount of waste Elk. If glass, aluminum and paper can all be recycled, why not scrap buidling materials?
There is currently a big push to do just that as part of LEED’s. Many new buildings are being specified to be LEED certified and part of LEED requires recycled products.
http://www.usgbc.org/DisplayPage.aspx?CMSPageID=1819
http://en.wikipedia.org/wiki/Leadership_in_Energy_and_Environmental_Design
LEED is purely voluntary although many (mabey most) Federal buildings are being specified to be LEED acredited many state buildings here in California are being specified to be LEED acredited to at least to the LEED Bronze level.
You can bet that states like Idaho, Arizona, and Utah are some of the last to specify LEED acreditation to their state buildings.
I am a Construction Engineer and have been in the building industry for over 25 years. The building industry is moving away from forest products. Forest products are not really needed anymore. Nearly all logging could end and building would continue with alternate building materials at nearly the same cost.
Here in California, the trend away from forest products is strong and it is for two main reasons.
Reason one is construction defect claims. There are many construction defects claims in California due to California’s consumer oriented laws that allow homeowners to sue for construction defects for up to 10 years after construction. Contractors, like doctors, buy insurance against law suits. The insurance rates for Type 5 construction (wood framing) are much higher than other types. The main problem with Type 5 construction is that it is susceptible to damage from water intrusion. A very small leak might lead to severe water damage and/or insect damage. It is a weakness of wood used as structure. Small amounts of water can destroy wood in just a few years. There are also mold issues. Wood is an organic material and if used anywhere in a building, organics can be carried inside by water intrusion and create mold problems everywhere. There are many mold spore lawsuits in California as well and architects and contractors are steering clear organic building material, including wood and paper (i.e. paper on sheet rock and insulation backing.) The added construction defect insurance cost of using wood and paper are only passed onto consumers and so market forces are driving wood products out of buildings, especially large commercial building where the stakes are higher and lawsuits more likely. It is rare to find even dimensioned lumber in a commercial construction project in California anymore and a new product called Densglass is displacing sheetrock for sheathing in all buildings. Densglass is like sheetrock but uses fiberglass in lieu of paper.
http://www.gp.com/build/product.aspx?pid=4674
Reason two is LEED’s….
http://en.wikipedia.org/wiki/Leadership_in_Energy_and_Environmental_Design
You can read about LEED above. It is purely voluntary and started with large scale, mostly public, projects but is now moving into residential and all forms of construction. It is becoming very common even in private buildings to be LEED certified. I actually studied to be a LEED’s Accredited Professional about two years ago but got caught up in learning some new software and had to give it up…for now. I will likely be required to become LEED’s accredited before much longer however.
The thing about LEED is that they promote the use of non-forest product building materials. The market for non-forest product building materials is being stimulated, as a result, and designers are coming up with innovative designs that do not use forest products. So much of the economics of construction is based on standards and standard methods. Because of predictability, because of existing skill sets, because of existing plants and equipment, the construction industry relies on standards and is slow to change. Change leads to unpredictability, problems with inexperience, requirements for new plants and equipment, and increases the probability of lawsuits. LEED’s is a way to accelerate change and it has, so far, been very successful.
So, do not believe we need forest products for the building industry. We do not. In fact, buildings are better if built from inorganic building material such as masonry, concrete, metal, fiberglass, and plastics that are insect proof, mold proof, fireproof, and not susceptible to water damage.
I worked for a couple of years on this Flight Projects Center at JPL. It won a LEED Gold Certification. I’ve worked on several LEED projects. I believe the total cost was about $110 million which is typical for a buiding of this size and type. One thing that made this building more expensive was the site. It was not a good site…hillside and old toxic waste from the Jupiter-C rocket era in the 50’s had to be abated by haz-mat companies. It added millions to the cost.
http://www.jpl.nasa.gov/news/features.cfm?feature=2198
http://blog.lpainc.com/lpa-blog/bid/27181/Displacement-Ventilation-Quietly-saving-energy-at-JPL
A lot of scrap can be recycled, the biggest problem is, the end result is more expensive and as long as that is the case, builders are going to continue to use new materials, as with many things, cost is the major driving force, glass aluminum and paper can be recycled with an end result that costs the same or less.
That is changing. You get LEED points for using recycled materials and this is creating a market and establishing an infrastructure for recyclng of building materials.
LEED’s has really been taking off here on the Left Coast. It will be everywhere in a few more years.
Just before I got out of the public accounting world, tax credits for LEEDS certification were really starting to take off. I did not work extensively on that tax issue, but it sounded like the tax savings were potentially substantial for builders.
Aren’t there like three or four different levels that you can attain based on how you build and the tax credit gets better the higher the level?
i designed one of the first LEED certified landscapes in Boise, up 15th street. good stuff.
Silver, gold & Platinum
I was not even aware that there were tax credits for LEED.
Most of the LEED buildings I worked on were Fed, State, or City buildings. Government building would not get a tax credit. Governments do it because politicians think it is simply a good idea…like subsidizing food production.
I just did a little research on tax credits. There are a few but only in a few cities or counties from what I can tell…might be something like a city beautification project some city council decided to approve. In general, private owners do it because they might save money on energy costs over the long haul and it might be good public relations.
I believe the hope is that some cities may simply require that building have some level of LEED-like building codes. Things are trending in that direction. With the energy savings, in many of the buildings the overall long-term cost of constructing and operating the building is nearly the same. Also, as some of these more green construction techniques develop, they will become more economical. If more forests are set aside and protected, lumber costs will increase and will also make green construction techniques more economical.
The goal of LEED is to change the economics of the building industry. Eventually, green building will be as economical as is conventional construction now but with many, many external benefits. Then, why not put many of these LEED type specifications into our national and international building codes? We already have codes for fire-life safety, for American with disabilities, for parking, for densities, and for aesthetics. Why not begin amending codes to preserve our forests and our environment in general?
Why move away from forest products?
Before anyone freaks on wood look at the energy requirements to produce the various materials….you will be amazed how much more energy is required to produce metal, concrete, plastic, etc…also putting wood into a build means you are locking away carbon and promoting new carbon storage in the growth of new trees…..cutting out wood means a great increase in your carbon footprint….
Many forest products still require substantial energy to transport and manufacture and the logs are comming from futher and further away.
I would rather have a few more nuclear power plants than lose any more forest. I hope so see clearcutting banned in the US in the next decade and see many logging roads removed and forests restored. They could start with Island Park and preserve it as part of Yellowstone for wolf and grizzly habitat.
Save bears Says:
September 23, 2010 at 11:55 AM
A lot of scrap can be recycled, the biggest problem is, the end result is more expensive and as long as that is the case, builders are going to continue to use new materials, as with many things, cost is the major driving force, glass aluminum and paper can be recycled with an end result that costs the same or less.
So SB, 4 tons of waste to build a house? Multiplied by how many new homes going up across the country? Gotta be a way to recycle that kind of waste and still manage to fine tune it enough cost wise, for a company to make a living at it.
Would that not put our species right up there with all the other species (that are considered far less intelligent) who have little or no impact on the planet, when THEY build a home?
And I have to mention, my best find to date at the local dump site (yes, I’m a dumpster diver and damn proud of it!) was a beautiful 7′ by 9′ braided, wool rug (went online and a rug that size would of cost me close to $500 dollars or more) and other than a couple of small stains, which came out in the wash over the back fence, I was clueless as to why it ended up in the dump – talk about waste.